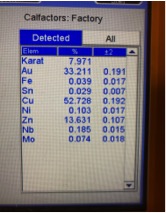
I’m often asked by both Pawnbrokers and Jewelers if I would suggest they purchase an XRF unit to help support their ability to accurately test scrap. These units can often be very pricey, so the most obvious consideration would point to the volume of Gold, Silver and Platinum scrap they’re dealing with and whether an expense like this is even warranted. Having an XRF unit should never be viewed as a replacement for old school testing (magnets and testing acid) that you’ve depended on for years, but as an additional tool at your disposal that also provides a non-destructive alternative in situations where scratch and acid tests are undesired.
To provide a full understanding of the benefits and shortfalls of this technology it’s important to understand how this instrumentation works. X-ray fluorescence is the emission of characteristic “secondary” X-rays from a material that has been excited by being bombarded with high energy from a primary X-ray or Gamma ray source. To put this in simpler terms as it applies to the application that we’re concerned about; as the instrument emits these X-rays at the surface of the sample being tested there is a secondary fluorescence (ionization of the component atoms) that is directed into a solid-state detector that analyzes the spectrum based on the unique energy of the photons for each element in the alloy being sampled. The accuracy and ability to provide repeatable results is directly linked to the unit’s ability to process as much information as possible, influenced by both the speed and voltage which the XRF unit operates. For example, the smaller table-top or hand-held Niton instrument you might be more familiar with will typically operate at around 3 volts with a detector speed of 2000 cps (counts per second). For comparison purposes Mid-States has an instrument that operates at 50 volts (allowing for more surface penetration) at a speed of 14,000 cps generating vastly more information for the detector to analyze, thus providing higher accuracy and repeatability.
In addition to huge differences in XRF hardware, there is equal disparity with their software, which in my opinion is the more important concern with these instruments. Most hand-held or smaller less expensive bench top units come pre-calibrated with factory installed software that cannot be customized for the specific application or range of elements in the alloys you’re testing. The larger more sophisticated XRF units come pre-programmed to allow for full spectrum analysis, but more importantly they enable the operator the ability to program their unit with multiple product sets that can be calibrated with any kind of laboratory grade Standards to match the specific application and elemental make-up for the samples they’re testing. Why is it important for you to understand this? When an instrument is analyzing a sample, it is forced to account for and report 100% of what it sees. But what if there’s an element or two contained in the alloy you‘re testing that was not accounted for in the instrument’s software and factory calibration? Well in this situation the XRF cannot recognize these elements but is also being forced to report a sum of elements that total 100%. So, to accomplish this it will include the value for the unknown in one of the other elements it’s reporting. Elements that are sometimes present in both jewelry and dental materials that might not be included in factory installed Standards on lower priced XRF units are: In, Cd, Pb, Sn, Ga, Ge, Cr, Co, Al, Nb. Depending on how that element diffracts during the X-ray, and it is not part of the Standard Set of the software, could potentially be mistaken for and added into a Precious Metal reading.
Proper preparation of the sample being inspected makes all the difference in the world if you expect XRF technology to provide any reasonable level of accuracy. You have to understand that you are only shooting the outer surface of the sample, with very minimal penetration below the surface. Therefore, to truly identify with any kind of reasonable accuracy, the percentage of Gold, Silver, Platinum or other, it’s absolutely necessary that the surface you are shooting is as flat as possible and of a properly cast homogeneous alloy, and not a plated surface or fabricated clad material (gold-filled). Without a clear understanding of the limitations of this technology and proper sample preparation you will run into several problems and develop a false sense of security that will lead to mistakes, often costly.
Illustrated below are XRF readings of some common materials that you frequently have coming into your stores. They are Gold Plated Brass/Copper, Gold Plated Sterling Silver (Vermeil) and 1/20 12 Kt. Gold-Filled. Before we start looking at these illustrations individually it’s important to understand that even though these readings are not true representations of the percentages of metal content by weight, these readings can be very helpful in actually identifying what the material is without the need for applying more destructive testing methods if you look for the proper clues. Now, looking at the XRF reading below for Gold Plated Brass we can see the Gold reading is below 10K but there is no Silver present and the Zinc content is 3X more than any jewelers alloy should have, so we can rule this material out as being any kind of typical karat gold. Actual Gold recovery on this type of material is in the range of 0.500% to 1.00%, but with the Gold-plated outer surface the XRF overstated the gold percentage by 30X, while the actual Copper percentage is most likely in excess of 90%. The picture showing the readings for Gold Plated Sterling Silver shows an overstatement of the Gold percentage which forces the Silver result to be understated. Actual Silver recovery for this material will be close to 92% with Gold running below 1%. The last picture below shows an XRF reading for a piece of stamped 1/20 12K Gold Filled, which should have a theoretical Gold Content of 2.50% but is reading 44% which could make an unsuspecting scrap buyer believe this could be 10K ; but with Nickel running in excess of 18% and it’s high attraction to a magnet are the indicators that help us avoid this mistake. The suggestion I hope you take away from this paragraph is to not just pay attention to what the readings are for the Precious Metals, when it’s often more important to pay attention to the other elements that are showing up or are present at abnormally elevated levels.
Gold-Plated Brass Gold Plated Sterling Silver 1/20 12K Gold-Filled
Lastly, even though XRF technology has improved in recent years you cannot forget this technology has its inherent limitations. Your instrument can be a very helpful tool, especially when you are limited to using a non-destructive testing method. However, you should not depend on a lower powered XRF instrument to have a consistent resolution of accuracy better than within + - 1% of what a Fire Assay will produce.